Demand management is essential for organizations and businesses to efficiently align their production and resources with customer demand. It plays a crucial role in optimizing operations, reducing costs, and enhancing customer satisfaction. By accurately forecasting and adapting to demand fluctuations, businesses can respond quickly to market changes, mitigate risks, and gain a competitive edge.
Demand management in SAP is a critical component of the enterprise resource planning (ERP) system. It enables organizations to effectively manage their demand, which helps maximize efficiency and limit overproduction.
Utilizing SAP’s demand management functions can help improve forecast accuracy, optimize inventory levels, and reduce costs.
Additionally, it gives organizations an understanding of how customer demands will evolve and how they must adjust their supply chain accordingly.
By utilizing demand management in SAP, companies can ensure that every aspect of their operations runs as efficiently as possible.
In this blog, we’ll explore demand management in SAP to streamline your supply chain and unlock efficiencies. We will also discuss its modules, demand management in PP, and advantages.
What is demand management in SAP?
Demand management is a set of features within Enterprise Resource Planning systems, such as SAP, which enable businesses to monitor and analyze customer demand, plan and manage inventory levels, and maximize efficiency.
Important features include data analysis, forecasting tools, cost reduction strategies, improved performance, automation tools, and successful case studies.
By understanding the fundamentals of demand management in SAP and following best practices for using these features, businesses can ensure that their operations are running as efficiently as possible.
Features/Modules of Demand Management in SAP
In SAP, the demand management module is used to plan, manage, and adjust production planning and inventory levels according to customer demand. The goal is to ensure that the correct product is available at the right time and place while minimizing waste and excess inventory.
The demand management in SAP modules includes features such as:
Forecasting
This tool uses historical data to predict future sales volume and schedule production accordingly. Accurate demand forecasting is a critical component of effective demand management in SAP.
- A demand forecasting tool can make this process easier by using historical data to predict future sales volumes and production schedules.
- This can help businesses plan and prepare for potential demand shifts.
- Such tools eliminate the need for manual demand forecasts so businesses can make well-informed decisions based on the available information.
- It helps them stay ahead of their rivals in volatile markets and provide quality products or services for their customers.
Some methods of demand forecasting
Macro-level demand forecasting
Macro-level demand forecasting helps businesses anticipate market trends, identify growth opportunities, and avoid potential risks.
It enables them to keep pace with global developments and cultural changes in their area of operation that may directly impact the success or failure of their business model.
Micro-level demand forecasting
Unpredictable market changes can create dramatic ripples of flux in demand for a particular product, region, or customer segment.
Micro-level forecasting allows companies to stay on top of minute deviations and adjust their strategies accordingly – ensuring an unexpected spike or dip never catches them off guard.
Short-term demand forecasting
One of the most critical aspects of running a successful business is anticipating consumer needs. Short-term demand forecasting can help managers plan for day-to-day operations by gauging customer preferences at both wide and local levels so companies remain competitive over limited timeframes.
Long-term demand forecasting
To ensure success in the future, businesses need to look beyond one year when planning their investments.
Long-term demand forecasting can provide an invaluable roadmap by evaluating things like expansions, enterprise investment opportunities, and potential new partnerships, helping organizations make decisions that will have lasting effects.
Production planning
This process determines how much of each product needs to be produced to meet customer demand. It also considers capacity constraints, supplier lead times, and other factors.
The Production Planning process is an integral part of the demand management workflow in SAP. This will integrate with other SAP modules like SD, MM, and QM.
- Its purpose is to evaluate customer demand forecasts, current stock levels, and more so that the precise number of each product is produced to meet demand.
- The process needs to consider capacity constraints, suppliers’ lead times, and other resources when scheduling and ordering materials for production.
- With accurate demand planning processes, businesses can reduce excess inventory, lower manufacturing costs, and increase customer satisfaction.
Structure of production planning
- Master data in SAP PP
- Production planning cycle
- Production planning process
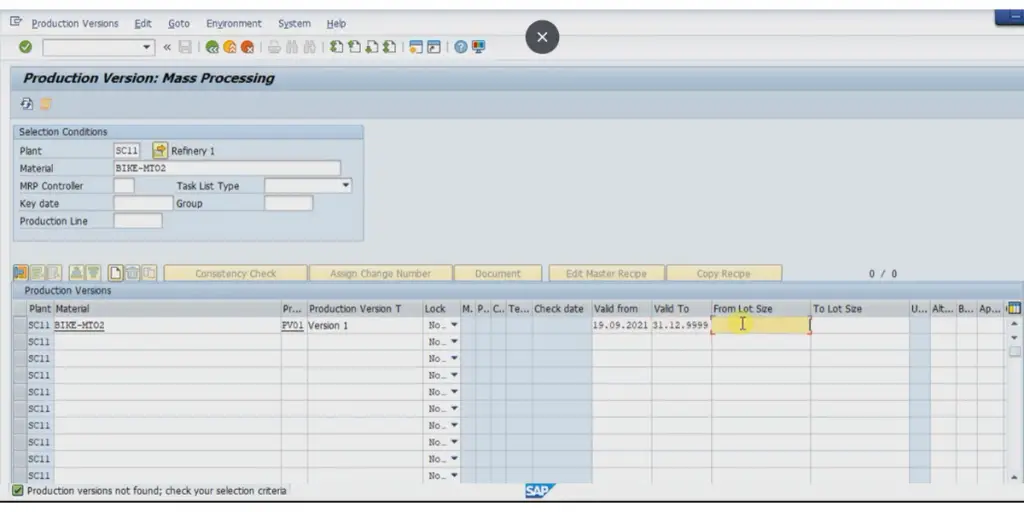
- Demand management
- Material requirement planning
- Capacity planning
- Order, confirmation, and closing
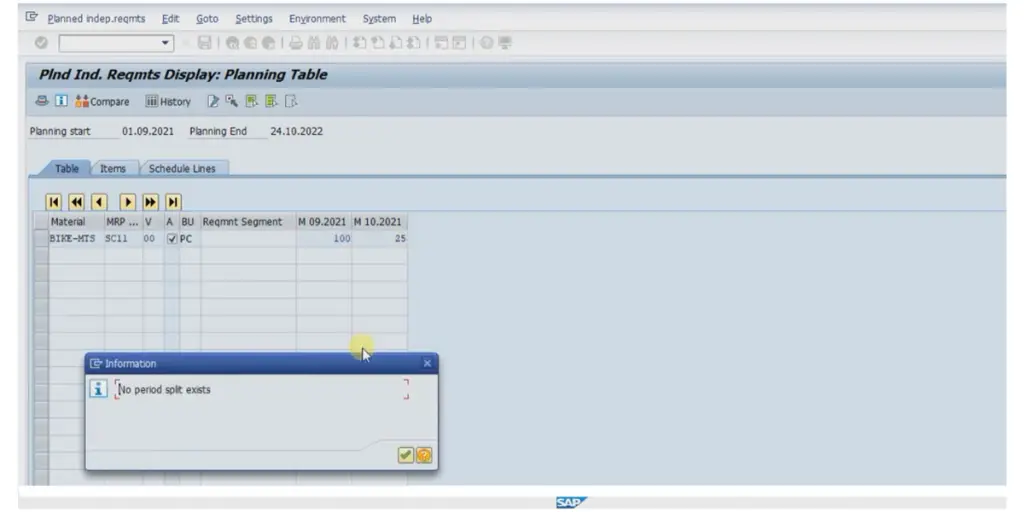
Inventory management
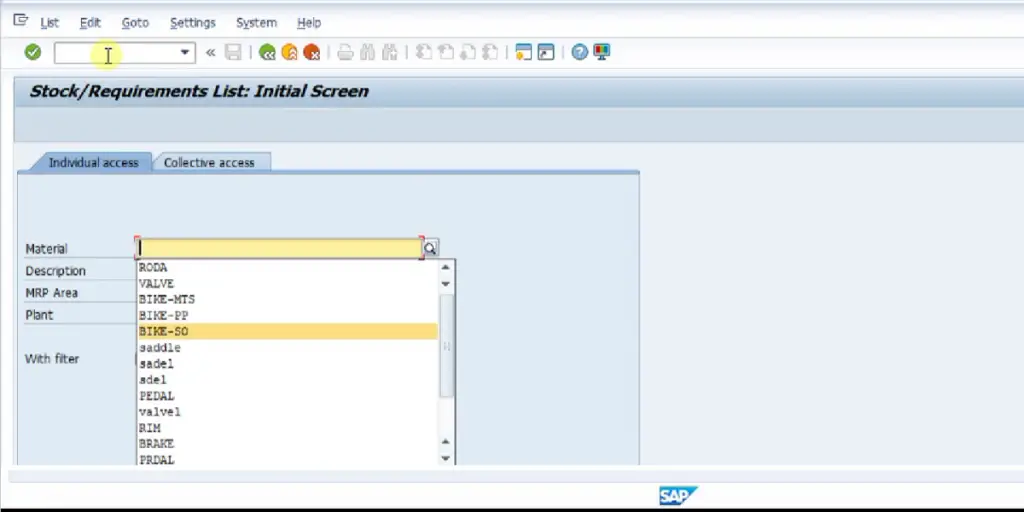
This system monitors stock levels and reorders products as needed to ensure that there is always enough inventory.
Inventory management plays a crucial role in demand management in SAP systems.
- Ability to monitor stock levels, determine product availability and demand, and trigger reorders when necessary.
- This system helps ensure that businesses across industries always have adequate customer inventory.
- By relying on accurate predictions and forecasting future demand based on past customer trends and usage behaviors.
- Businesses can be sure they’re ordering the right inventory to satisfy demand.
SAP inventory management mainly concentrates on the movement of goods.
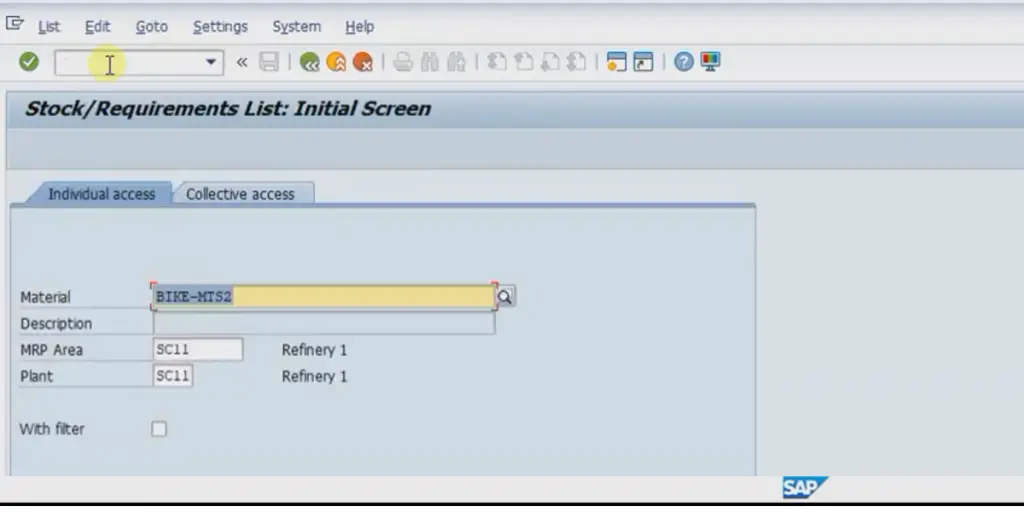
Primary inventories are classified below.
- Goods receipts
- Goods issue
- Internal movements
Demand management in SAP PP (Production Planning)
Demand management in SAP PP can be complex, but understanding the technology behind it can make it much easier to manage.
Planned Independent Requirement (PIR)
Planned Independent Requirement (PIR) is the technology that offers demand management in SAP PP.
- It helps supply the input for production planning by having one planned quantity of a product and one date for material or splitting a planned quantity over multiple timeframes.
- Using PIR helps provide an accurate demand plan, which helps ensure production quantities are just right and low enough.
- By understanding how demand management program works with this technology, businesses can ensure they’re able to meet customer demand while avoiding wasting resources on overproduction.
Production Independent Requirement(PIR) technology follows some strategy for demand management. They are
Make-to-order strategy (MTO)
Demand management in SAP heavily depends on a make-to-order planning strategy, which is why stock and products are only generated when sales orders from a specific customer have been received.
- This allows for an effective demand planning process that ensures stocks and production processes are not being carried out for products the company does not need.
- With MTO planning, finished products are produced once the company receives the sales order – allowing teams to calculate demand and better manage their resources properly.
Make-to-stock
Make-to-stock planning strategy is a demand management system developed in SAP. It creates and stocks inventory beforehand to meet future customer demands.
- The key components are that the PIR quantity is considered for MRP run, but sales orders are completely neglected; this is signified by the associated requirement type, which gets reduced when any stock is delivered to the customer.
- This approach effectively ensures demand is met quickly and efficiently, given the right amount of available stock.
Advantages of SAP demand management module
Demand management in SAP is essential for organizations seeking greater visibility into demand and inventory planning processes.
- By leveraging a demand management solution like SAP, organizations can employ an integrated approach to demand and supply chain planning, enabling them to forecast demand accurately.
- With lower inventories, reducing costs while ensuring adherence to customer demand patterns.
- With SAP’s demand management capabilities, businesses can improve accuracy and optimize their inventory levels, saving time and money through better demand forecasting.
- Ultimately, utilizing a demand management solution like SAP accelerates the entire planning process, resulting in increased profitability and customer satisfaction.
FAQs
What is the main issue of demand management?
A big problem for organizations is that they cannot get accurate information about what people want. This leads to too much stock, which goes against having a lean supply chain.
What is the demand planning process in SAP?
Demand planning in SAP involves using the software’s integrated tools and processes to forecast and manage product demand. It encompasses activities like data collection, statistical forecasting, collaborative input, and consensus-building to create an accurate demand forecast. SAP’s demand planning process allows organizations to fine-tune their production, inventory, and supply chain strategies, ensuring that they align with customer demand.
Conclusion
This blog post provided detailed information about demand management and how the SAP module can help organizations with this crucial task.
A demand management solution like SAP can help your organization improve overall forecast accuracy, optimize inventory levels, and reduce costs.
We hope that you found our guide to be helpful and informative.