For the smooth flow operations in the business world wherein, the supply should meet the demand, inventory management plays a crucial role.
It is not just about storing the commodities; it is a well-organized plan that helps you use resources wisely, cut costs, and make everything work better.
Think of it as the protector of the balance between having too much and too little—a constant juggling act that keeps businesses going strong.
This post will uncover what inventory management is, its techniques, systems, and types of inventory.
Check your order up to level with our easy Online calculator for Order Up to Level.
Evaluate your inventory turnover ratio using our Inventory turnover ratio online calculator
What is Inventory Management?
Inventory management is the process of tracking and managing your company’s inventory. This includes items that are currently in stock and those that are on order.
Having a system for managing your stock is important because, without it, one can end up losing money fast. Regrettably, many businesses fail because they lack an efficient system in place.
There are several vital components to it, including:
- Tracking your inventory levels
- Knowing what items you need to order
- Managing your warehouse space
- Keeping track of your inventory costs
Each of these components is important in its own right, but they all work together to ensure that your company’s inventory is managed effectively.
What are Inventory Management Systems?
Inventory management systems are computer software that helps businesses in the inventory management process. Typically, companies will use these systems for periodic inventory control.
ERP (enterprise resource planning) and warehouse management software are the most common inventory management systems. ERP software is used by businesses that have multiple locations or supply chains.
In contrast, warehouse management software is used by companies that operate warehouses and need to track the movement of goods in and out of their facilities.
Inventory Control in Supply Chain Management (SCM)
Inventory management manages the flow of goods and materials through the supply chain to meet customer demand. It includes forecasting demand, ordering goods, deciding when to produce or purchase specific items, and ensuring correct inventory levels.
It is critical to SCM because it helps ensure that the correct amount of inventory is available to meet customer demand. If too much stock is built up, money is wasted on storage costs, and it may be challenging to sell the excess items.
On the other hand, if too little inventory is maintained, customers may not get the things they need when needed, which can lead to lost sales.
Click here for our online Storage Costs of Inventory Calculator
Aspects of Inventory Management
1. Tracking Inventory Levels
One of the most critical aspects of inventory management is tracking your inventory levels. This helps determine how much stock you have on hand and how much you expect to receive soon.
If you don’t track your inventory levels, you cannot know when to order more stock. This could potentially lead to lost sales and wasted money on inventory that you don’t need.
A few ways to track your inventory levels are:
a. Manual Inventory Counts
This involves physically counting the number of items in your inventory. This can be time-consuming, but it’s the most accurate way to track your inventory.
b. Inventory Tracking Software
Inventory management software is a type of software that helps businesses track and manage their inventory. For example, it can help companies keep track of what items they have in stock, how much stock they have of each item, and when items are due to expire or run out.
Some inventory management software also allows businesses to track orders and sales. This can help enterprises see what items are selling well and which items they might order more.
Additionally, some solutions can generate reports that show how much money a business has made from its inventory.
c. Inventory Reports
Most accounting software programs include reports that track your inventory levels. This can be a helpful way to get an overview of your stock levels, but it may not be as accurate as a manual count or Inventory Tracking Software.
2. Knowing What Items You Need to Order
Another vital aspect of inventory management is knowing what items you need to order. This includes regular orders for items you keep in stock and special orders for items you only need occasionally.
If you don’t know what items you need to order, you may order too much or too little inventory. This can lead to lost sales or wasted money on excess inventory.
Few ways to know what items you need to order,
a. Inventory Forecasting
This is the process of predicting how much inventory you will need in the future. This can be done manually or with the help of inventory tracking software.
b. Sales Reports
Most accounting software programs include reports that track your sales data. This can help you see which items are selling the best, and it can help you determine how much inventory you need to order.
c. Inventory Lists
A well-organized inventory list can help you see which items you are low on stock and which items you need to order. This can be helpful if you don’t have access to sales data or if your accounting software doesn’t include Inventory Management features.
3. Managing Your Warehouse Space
Another important aspect of inventory management is managing your warehouse space. This includes knowing how much space you have and how to utilize that space best.
If you don’t manage it properly, you may have too much or too little inventory. This can lead to lost sales or wasted money on excess inventory.
Few ways to manage it,
a. Inventory Spacing
This is the process of spacing your inventory items to be easily accessed. It also includes organizing your inventory, so it’s easy to find what you need.
b. Inventory Racks
Using racks can help you maximize your warehouse space. Shelves come in various sizes and can store all shapes and sizes in inventories.
c. Inventory Shelves
Shelving is another excellent way to utilize your warehouse space. Shelves can be used to store inventory that is not being used and inventory that needs to be shipped.
Types of Inventory
Inventory type depends upon the industries and their operations — the inventories in the merchandising sector store the end product.
In manufacturing industries, the inventory has raw materials along with the sub-assemblies.
Below are the types of inventory,
Raw Materials
The manufacturing process that produces subassemblies or final products uses raw materials. Warehouse stocks these raw materials that are available for production.
Work-in-progress/Subassemblies
This type of inventory consists of materials like raw and component materials. The manufacturing process utilizes these materials for its end product.
Once the final quality check is over, these materials are part of the finished goods.
Click here for the Work-in-progress calculator
Finished Goods
The finished goods are the end products that have completed the manufacturing or production process and are ready to be sold to customers. Supplies and dealers use the finished goods inventory to store the bought goods.
MRO Goods
MRO stands for Maintenance, Repair, and Operating. The product includes the necessary items used for maintaining and repairing work.
You can see examples of MRO inventory in the clothing industry. This industry usually provides extra items like buttons with the finished product.
Transit Inventory
Shipment and movement of goods are essential in most companies. This type ships the goods and transports them to different warehouses.
Buffer Inventory
Buffer inventory stores the buffer stock to meet the forecasted demands. As a result, buffer inventory reduces out-of-stock situations and ensures proper business to customers.
Click here for the Buffer stock calculator
Decoupling Inventory
This inventory works for manufacturing units. The production process is usually coupled with many methods.
These processes are interdependent. The decoupling inventory separates the inventories of another method.
Cycle Inventory
This type is for a standard business cycle. For every process, the manufacturing of a regular amount of product occurs.
Inventory Management Techniques/Methods
For any industry managing the inventory is an important task. There are different techniques to manage inventories efficiently. These are useful in maintaining the profit of a business.
1. Just in time (JIT)
The company stores the exact amount of inventory required for production, avoiding storing the excess.
This technique saves the cost of storage and insurance for the items. In addition, the new stock buying needs to happen only when the older stock is close to replenishment.
This type of management technique is called “zero inventory.” In this type, an order initiates the cascade of events needed for production.
It reduces waste, eliminates stockpiling, and maximizes efficiency by maximizing inventory turnover.
2. Minimum Order Quantity
It allows you to order the lowest set of amounts of stock a supplier is willing to sell. You cannot buy the item if a supplier is unwilling to sell below the minimum quantity.
Stronging the stock for some time results in a delay in realizing the profit. This method helps the suppliers to maintain a healthy cash flow.
3. ABC Analysis
ABC stands for Always Better Control Analysis. The inventory items are classified into A, B, and C categories. The items in the A category are expensive and strictly controlled.
B category is less expensive as compared to A and is moderately controlled. On the other hand, C-category items require more secondary investments and are highly available.
So the control level of the C category items is minimal.
Click here for the ABC Classification Calculator
4. FIFO and LIFO
In the case of FIFO ( First-In-First-Out), the first utilization happens for the first entered items. The food industry observes this kind of management technique.
In this process, the consumption of the first-in-perishable items happens first.
The LIFO (Last-In-First-Out) technique is for non-perishable and homogenous items. These goods are easy to manage and do not need a re-arranged warehouse for each batch or order.
Click here for the Inventory Value Calculator
5. Materials Requirements Planning (MRP)
Material Requirements Planning (MRP) is a systematic approach to managing and planning the materials needed for the manufacturing process. It helps organizations ensure they have the right materials available at the right time to meet production demands.
More on Material Requirements Planning.
6. Economic Order Quantity (EOQ)
Economic order quantity helps to reduce inventory by ordering the lowest amount of stock. As a result, it saves the storage cost and achieves the target during peak demand hours.
This method is the safest. However, it does not drain the inventory items and achieves the required target.
According to Kenneth Boyd, the calculation of EOQ is,
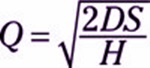
EOQ uses three variables,
D = Demand in the units required for the production
S = Ordering cost per purchase
H = Carrying cost per unit
Click here for the Economic Order Quantity Calculator
7. Safety Stock Inventory
Base stock is stored to deal with the market variations of particular items. This technique deals with serious unexpected business issues.
It stores just the required amount of inventory before completely drying out.
It prevents stock-out and protects against unexpected spikes and demands. In addition, it buffers the stock and helps compensate the inaccurate market forecasts.
Safety Stock Inventory = (Max Daily Sales x Max Lead Time in Days) – (Average Daily Sales x Average Lead Time in Days)
Click here for our online Safety Stock Calculator
8. Dropshipping
Dropshipping is in the supply chain management system where the merchant neither owns nor stocks the goods.
Once the merchant receives an order for the goods, the supplier gets the requirement.
The supplier ships them to the customer on behalf of the merchant. This type does not require inventory; the order fulfillment cost is low. Therefore, this type’s risk is low, and the startup cost is low.
Read dropshipping trends.
9. Consignment Inventory
It is a business deal between the consignor (vendor) and the consignee (retailer). The consignor delivers the items to the consignee without advance payment.
The consignee pays the amount only after selling the items. It is a win-win situation for both. It improves the cash flow and enhances the partnership between them.
10. FSN Inventory
FSN stands for Fast, Slow, and Non-moving inventory items. Therefore, not all the things required for production are needed frequently.
This method classifies the inventory into Fast-moving, Slow-moving, and Non-moving inventory. In addition, it allows you to order the required amount of inventory items based on utilization.
11. Reorder Point Formula
Reorder point formula identifies the right time to order the inventory item.
More on reorder point.
Click here for the Reorder point calculator
12. Batch Tracking
Batch Tracking is known as a lot-tracking process. This is because it efficiently tracks the goods using batch numbers and other details.
13. Perpetual Inventory Management System
A perpetual inventory management system is also known as a continuous inventory system. This inventory system tracks the sold and stocked items in real-time.
It helps multiple departments to track the items. For the perpetual method, ERP inventory modules are prevalent.
More on Perpetual inventory management system.
14. Lean Manufacturing System
It is known as lean production. It is a system to maximize product value and minimize waste.
It is a Toyota Production System developed to eliminate three types of deviations. These deviations lead to the inefficient allocation of resources.
These three types of deviations are Muda (waste), Mura (unevenness), and Muri (overburden).
Using the lean manufacturing system, companies adhered to 5 principles. These are,
- Value
- Value Stream
- Flow
- Pull
- Perfection.
The organizations integrate the “lean manufacturing techniques” with these. This combination has been observed to produce the best quality products.
15. Sigma and Lean Six Sigma
This is a data-driven process. As a result, the product defects are reduced to 3.4 defective parts per million. Therefore, this method enables us to deliver a perfect product.
Statistical models are used to study the data of the given industry. These models help improve the process’s performance until they achieve the Six Sigma level.
There are two different ways to implement the Six Sigma model.
- DMAIC: The 5 step process is called DMAIC. It stands for Define, Measure, Analysis, Improve, and Control. This method is used to improve the established process.
- DMADV: This is mainly used to develop a new process. DMADV stands for Define, Measure, Analyze, Design, and Verify.
Lean Six Sigma is the fusion of Lean Manufacturing and Six Sigma.
16. Demand Forecasting
It predicts what the customers may buy, the quantity, and the time. The prediction depends on previous experiences, guesses, or sales data.
Demand forecasting assists in the decision-making process during the critical stage.
Click here for the Single Exponential Smoothing Forecast Calculator
Example of Inventory Management
Here, we are taking an example of just-in-time inventory management.
AromaKing is a bakery nestled in a bustling neighborhood, where the aroma of freshly baked bread wafts through the air, enticing passersby. In this delightful establishment, the bakery owner has perfected the art of just-in-time inventory management to craft a seamless and efficient operation.
Let us see how they implemented just-in-time inventory management.
Each morning, the skilled bakers carefully calculate the day’s demand based on past sales trends and current customer preferences.
Rather than stockpiling vast quantities of ingredients, the bakery maintains a lean inventory, strategically aligning supplies with anticipated orders.
The bakery has established strong relationships with local suppliers who understand the importance of precision in their deliveries.
Through regular communication and real-time updates on inventory levels, the suppliers ensure that the bakery receives the exact quantities of flour, yeast, and other ingredients just in time for the day’s production.
With just-in-time inventory, the bakery achieves a delicate balance—ensuring that each pastry, loaf, and croissant is not only made to perfection but is also incredibly fresh, enhancing the overall customer experience.
By avoiding excess inventory, the bakery minimizes the risk of unsold items reaching their expiration date. Using a just-in-time approach allows the bakery to focus on producing high-quality goods without having to store excess inventory.
Following just-in-time inventory management helps the bakery to quickly experiment with new products. If customers request a new item or if the season changes, the bakery can easily adjust its production schedule.
Benefits
Strategic Cost Control
Inventory management allows businesses to optimize costs by preventing overstocking and minimizing holding costs. It is not just about storing goods; it’s about smartly investing in the right amount of inventory to meet demand without unnecessary expenses.
Customer Satisfaction Through Availability
Ensuring products are consistently available translates to happy customers. Inventory management ensures that shelves are stocked when customers want to make a purchase, contributing to increased customer satisfaction and loyalty.
Space Optimization and Efficiency
Inventory management optimizes warehouse space and improves operational efficiency. Every square foot becomes a valuable asset, contributing to a streamlined and cost-effective operation.
Enhanced Supplier Relationships
Through accurate demand forecasting and timely orders, businesses can build strong relationships with suppliers. This not only ensures a steady supply of materials but can lead to favorable terms, discounts, and collaborative partnerships.
FAQs
What is the difference between Inventory and Stock?
People often use the words “inventory” and “stock” to mean the same thing, but they have some important differences in business. Think of them like siblings in a family—they’re related, but each has its own job.
Inventory is the comprehensive term encompassing all assets a business holds, from raw materials and work-in-progress items to finished goods ready for sale. It’s the entire spectrum of resources a company manages throughout its production and distribution processes.
On the other hand, stock is the subset of inventory that specifically refers to finished goods or products ready for sale.
Conclusion
Inventory Management is a critical part of running a successful business. By tracking your inventory levels, knowing what items you need to order, and managing your warehouse space, you can ensure that you always have the right amount of inventory. This will help you avoid lost sales and wasted money on excess inventory.
References