Aggregate planning stands as the cornerstone in the world of strategic business management. As businesses navigate the ever-evolving landscape of demands, resources, and market fluctuations, mastering the art of aggregate planning becomes an imperative.
It is a business strategy that helps companies plan how to use their resources and produce what people want in the future.
This blog post will define aggregate planning and discuss its benefits, strategies, and examples. We’ll also provide some tips on creating an effective aggregate plan.
Definition
Aggregate planning is a way to plan the production of all products for a company over a period of time. It starts by listing all the important requirements for uninterrupted production. The usual planning horizon ranges from three to twelve months.
The word ‘aggregate’ comes from the Latin word ‘aggregāre.’ It means ‘to add to.’ It is frequently used in economics or business. This is why aggregate production planning is the exercise of developing an overall production schedule for all products combined for a company.
Aggregate planning does not differentiate colors, sizes, and features. For example, in a mobile handset manufacturing company, aggregate planning considers only the total number of handsets, not the separate models’ colors.
Aggregate Planning Example
Imagine a company making multiple products, where the demand for some goes up while others go down. Instead of predicting each product’s sales separately, combining these forecasts offers a clearer picture of overall demand.
It’s like blending ingredients in a recipe; while individual flavors may vary, the mix tends to balance out. By focusing on an aggregate production plan that considers all potential shifts in demand, the company can better prepare for the future, ensuring it allocates resources like people, machines, storage, and raw materials effectively.
The planning covers various elements, such as
- Human resources
- Raw material
- Financial planning
- Operations
- Engineering
- Marketing and distribution
This comprehensive approach serves as a vital tool for companies, aiding in the optimization of immediate production processes. By harmonizing these processes with the organization’s long-range plans, it ensures strategic alignment and facilitates efficient operations.
Importance
- It helps to reach financial goals by decreasing overall variable costs.
- It reduces the cost of inventory stocking.
- It helps to utilize the maximum available production capacity.
- It helps achieve the demand on time and reduces the customer’s waiting time.
- It enables the organization to meet scheduled goals and satisfies workforce planning.
Types of Aggregate Planning Strategies
Two types of aggregate planning strategies are level strategy and chase strategy. The third approach is utilizing the best of both methods.
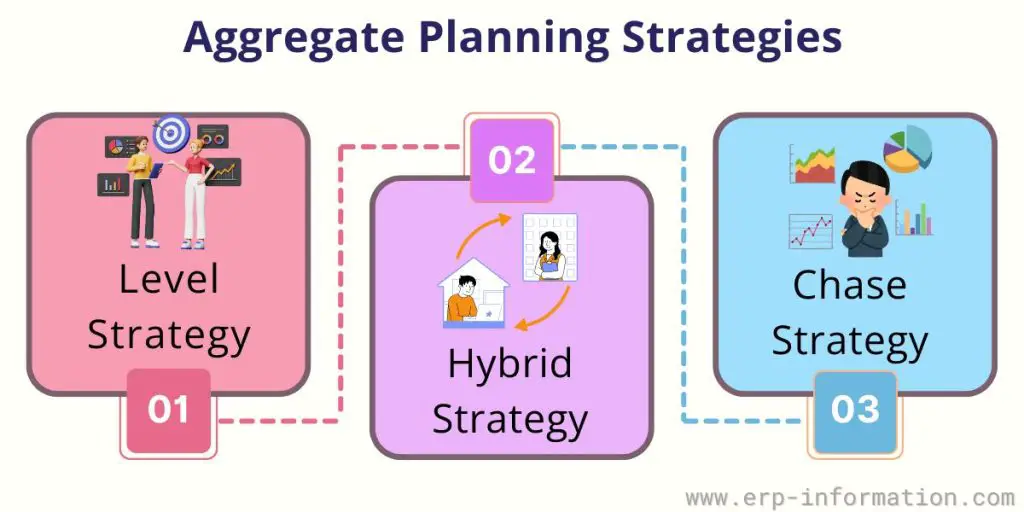
Level strategy
This is also known as a production-smoothing plan or a stable plan.
It focuses on maintaining consistent production levels and managing the workforce within a company. The expected demand rate is achieved by adjusting various factors, such as financial resources and the utilization of human capital.
Though this strategy helps maintain human resources, it also stocks inventory. There are also chances of not meeting the expected targets, resulting in backlogs costing a lot more to the firm.
The level strategy is best suited to situations where inventory carrying costs are not high.
Read more on Level Production Strategy
Chase strategy
It is also known as a just-in-time production plan.
Just in time (JIT) is a manufacturing methodology designed to decrease waste by receiving goods only as needed. JIT was developed in Japan to make the best use of limited resources.
It focuses on matching the anticipated demand with rigorous production. Unfortunately, though this strategy aims to meet the market, it usually results in stressed employees, which increases attrition.
This strategy is best suited to situations where the cost of changing the production rate is relatively not high.
Read more on Chase Production Strategy
Evaluate Chase production strategy using our Online Chase production strategy calculator
Hybrid strategy
A hybrid strategy in aggregate planning uses a combination of methods to arrive at the final production plan.
For example, a company may use a mathematical model to calculate the optimal production plan and then adjust it based on their actual production process feedback. The combination gives them the best of both worlds – the accuracy of a level strategy combined with the flexibility of a chase strategy.
The hybrid strategy blends both level and chase strategies for better and more fruitful results.
The hybrid strategy in aggregate production-planning balances production rate, hiring/firing, and stock level.
What is the Criterion that Influences Aggregate Planning?
- Is the hiring and firing of employees allowed?
- Is overtime allowed based on the fluctuation in demand?
- Are backorders allowed?
- It is crucial that before planning, complete details about the product must be collected and analyzed. The inventory and production capacity have to be thoroughly understood.
- A reliable demand prediction helps in planning better.
- Every process of the firm contributes to successful aggregate planning. Therefore, all organizational factors must be considered, from quality control to labor morale management.
- Proper financial management ensures appropriate costing.
It assures that all production factors are thoroughly examined to achieve the firm’s goal.
Two main factors while calculating aggregate planning are aggregate demand and aggregate capacity.
Aggregate Demand and Aggregate Capacity
Aggregate planning starts with the establishment of aggregate demand and aggregate capacity.
What is aggregate demand?
Aggregate Demand (AD) is the quantitative assessment of the requirement for all goods and services at a given price level for a specific period.
The demand curve depicts the correlation between the price level and the demand. In addition, it is observed that both factors share a hostile relationship called “total spending.”
It is understood that when the price level of a product or a service is high, the demand for the same goes down, and when the price level is low, the market steadily increases.
What is the aggregate capacity?
Aggregate capacity is the required or available capacity to carry out a function.
The process of ascertaining the company’s overall volume and ability to perform its entire resources is called aggregate capacity management. The steps involved in aggregate capacity management are
- Understanding the aggregate demand and supply for a specific period
- Preparation of suitable plans and contingency plans for situations where the demand levels might fluctuate
- Finalizing an appropriate plan
An organization needs to understand the capacity of its resources. That will help the business know its production capacity, leading to proper sales forecasting and prompt supply of products to the customers.
That will also ensure the right balance between the demand and supply without stressing the resources.
The resources can vary from company to company, but aggregate capacity considers manual and machinery resources and does not differentiate between the two.
For instance, if the company is into the production of bikes, the aggregate capacity will consider only the end product numbers.
It will not consider the complexity of each bike, the variations, and the specialties. Instead, it looks from a macroscopic view.
Aggregate planning becomes successful when both aggregate demand and aggregate capacity are equal.
When there is an imbalance between them, the organization must decide whether to add or reduce capacity to attain demand or add or reduce the need to achieve capacity.
Here are some tips to increase demand to meet the available capacity.
- Price: Lessen the cost of the product or service to increase the demand. For example, cloth industries offer discount sales at the end of the season to increase demand. Some hotels also fix seasonal rates to attract customers.
- Advertise: Many companies promote their products through advertising and direct marketing.
- Generate new demands: Industries like hotels and bars offer some complimentary services to create some extra demands. Likewise, grocery shops offer home delivery services to create demand.
- Backorders: To smooth the demand, some companies shift the current orders to the next period when the capacity is not used correctly.
Here are some tips to increase or decrease the capacity to meet the existing demand.
- Overtime: The organization can create additional capacity by making the employees work extra time in a day or work another day per week. It is an excellent choice to increase capacity without much investment in hiring workers.
- Hiring or firing workers: It is one of the ways to make capacity and demand balanced. The company can hire employees to increase the capacity required for the increased demand or fire some current employees to decrease the capacity for reduced demand.
- Part-time workers: The company can hire workers on a contract or on-call basis to meet the demand.
- Final product inventory: It is one of the common methods companies use. The company can stock the finished products when demand is less and capacity is high to use those products to fulfill the current demand without increasing the capacity.
- Sub-contracting: The organization can obtain temporary capacity by subcontracting to another manufacturer or service provider.
- Cross-training: Train the employees so that they will be able to do not only their work but also they can do some flexible work if it is needed.
How to manage demand fluctuations through aggregate capacity management?
Generally, the business will have pure strategies ready to meet such unexpected situations. However, a combination is also used based on the needs.
- Altering the size of the workforce: This involves getting more people to work or laying off people when there is an excess of resources.
- Altering the usage of human resources: Utilizing the existing workforce by providing overtime, incentives, and such schemes.
- Changing the size of inventory: Depending on how much the production can be leveraged, the inventory is ordered.
- Outsourcing, sub-contracting, varying the plant capacity: Passing on the work and meeting the production requirements
Objectives
- Decrease expenditures in different inventories
- Increase the usage of devices and equipment
- Decrease the variations in the production rate
- Provide good customer service
- Decrease the workforce level variations
- Decrease the cost of planning outline
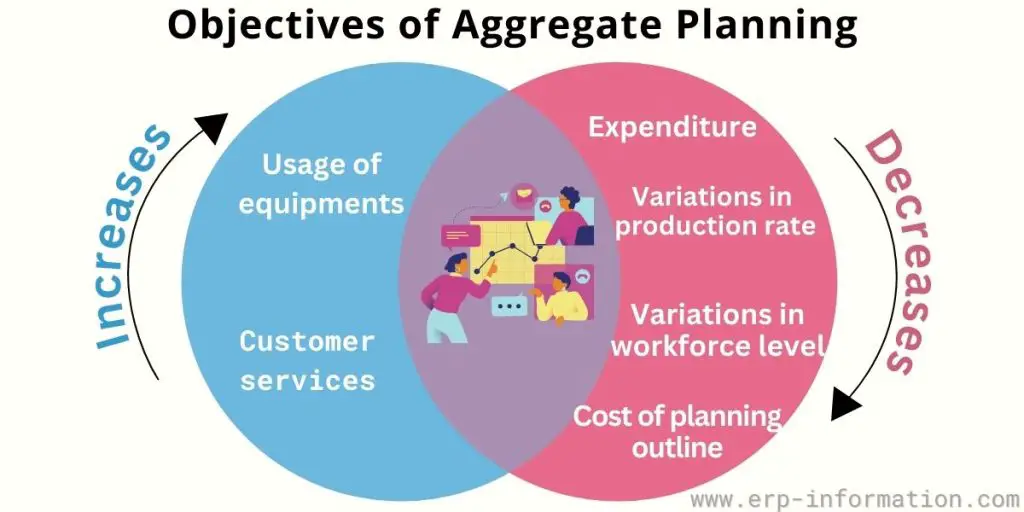
Challenges
Limited time range
- Short-term focus may lead to neglect of long-term goals and strategic initiatives.
- It necessitates frequent revisions to accommodate changing circumstances, which can be resource-intensive and disruptive to operations.
Assumption of stability
- Aggregate planning often assumes a level of stability in demand, supply, and other factors, which may not align with the dynamic nature of many business environments.
- Unexpected disruptions such as natural disasters, economic downturns, or supply chain disruptions can render the plan ineffective or obsolete.
Balancing conflicting objectives
- Aggregate planning involves trade-offs between various organizational objectives such as minimizing costs, maximizing utilization of resources, and meeting customer demand.
- Finding the optimal balance among these objectives while considering constraints like capacity limitations and labor regulations can be intricate and require sophisticated decision-making processes.
Human resource considerations
- Adjustments in workforce levels and scheduling to align with aggregate plans can pose challenges in terms of employee morale, job satisfaction, and labor relations.
- Layoffs, temporary shutdowns, or changes in working hours may lead to resistance or discontent among employees, affecting productivity and organizational culture.
Aggregate Planning Flowchart
The Mathematical Approach to Aggregate Planning
We will list some mathematical techniques used in more composite aggregate planning applications.
Linear Programming
It is one of the refinement techniques that help the customer generate more revenue with minimum resources or available capacities.
The transportation model (special linear programming) allows customers to balance capacity and demand with minimum cost.
Mixed-inter Programming
This technique will be helpful when the aggregate planning is intrinsically the sum of plans for individual production lines.
In this case, mixed-integer programming allows finding out the number of units produced in each production line.
Linear decision rule
It is one more optimization technique. It helps attain a single quadratic equation by using cost-approximating functions ( three of them are quadratic) to reduce production costs.
Then you can derive two linear equations from that quadratic equation and use one equation for planning the output for each period and another for planning the workforce for each period.
Management co-efficient model
This method is formed on the production rate for any period that this equation will set
ie P t = aW t-1 − bI t -1 + cF t+1 + K, where a,b,c,K are constants and using regression analysis you can find their values.
P t – the production rate set for period t
W t – 1 – is the workforce in the past period
I t-1 – the ending inventory for the past period
F t+1 – the forecast of demand for the next period
Search decision rule
This technique helps overcome some of the limitations of linear programming techniques about cost assumptions.
It enables the customer to express cost data inputs in standard terms. First, it needs computer programming to evaluate any production plan’s cost. Then it searches for alternative methods with minimum prices among them.
Advanced planning and scheduling (APS) software can quickly assist in aggregate planning. APS is a process that enables organizations to plan and schedule activities more precisely.
This process helps to keep the total cost of an organization’s projects low by minimizing disruptions caused by unplanned events.
APS uses two main techniques: Activity duration in project management (DPM) and work progress tracking (WPT). DPM involves using past data on past project tasks to predict future task durations; WPT involves monitoring assigned tasks and taking corrective action when necessary so as not to interrupt current work assignments.
FAQs
Why is aggregate production planning needed?
The demand for the various products of a company could vary. If the need changes, how do you commit your resources to meet this variation in the market? So, to balance the variations aggregate planning is needed.
Conclusion
Aggregate planning is a method of planning for the future. Organizations should use it to help them understand how their current activities will affect other areas soon and what could happen if they change their strategies or policies.
There are many benefits to using a holistic process. These include increased efficiency, lower costs, improved innovation and creativity, and reduced risks from unanticipated events. However, there are also some drawbacks, such as the high upfront cost and complexity.
References: