PPB is a heuristic that can be used to optimize lot-sizing.
The PPB algorithm balances the benefits of producing larger quantities (lower unit costs and shorter cycle times) against the increased inventory-carrying costs associated with producing and holding more inventory.
This blog post will discuss how the PPB heuristic works and how you can apply it to your organization’s production planning processes.
What is Part Period Balancing?
Maintaining an efficient production schedule is essential for any business. However, minor inventory discrepancies can lead to missed deadlines and dissatisfied customers.
As a result, many companies rely on Enterprise Resource Planning (ERP) software to help them keep track of their parts and products.
Part period balancing (PPB) is a lot-size technique using look ahead and look back functions to consider additional periods in modifying an initial calculation based on the least total cost.
Material Requirements Planning (MRP) is integral in today’s ERP systems.
MRP manages the production programs for finished and unfinished products. In addition, MRP monitors inventories and facilitates determining the specific quantity of material needed at a given date.
During this process, the calculation for available or planned stock requirements is compared with the primary requirements.
As the available inventory gets lesser than the required quantity, the MRP system initiates make-or-buy decisions by generating a procurement proposal.
It also plans the order according to the changing date and quantities. In case of a shortage of materials, it must quickly adjust to the new requirement of procurement of materials.
MRP acts as an interface between demand and production planning and chooses the correct lot size for planning production.
Lot Size
The lot size is determined by the machine batch size, customer order, and production. The Part Period Balancing heuristic method helps to find an optimal balance between products in each manufacturing stage to be efficiently produced while maintaining inventory levels at a minimum.
Lot size determines the quantity ordered during production. Lot sizes can be fixed or dynamic and are determined by the machine batch size, customer order, production size, and shipment size.
ERP systems are inbuilt with multiple heuristic methods to determine the lot size for the production unit. One of them is a Part Period Balancing heuristic method.
Part Period Balancing Heuristic Method
Part Period Balancing (PPB) method of lot-sizing minimizes the sum of ordering costs and inventory carrying costs for a single item.
In this method, the successive requirements of an item starting from the shortage date are grouped to form lots whose sum is less than equal to the lot size-independent cost.
We’ll consider an example of the item to be purchased for $20, lost size-independent costs: $100, and storage cost percentage: 10%.
Storage cost = Requirement * Price * Storage cost % * Time in Storage / 365
Requirement Table:
Calculations for Storage Cost:
Storage Cost = (1000 * 20 * 0.1 * 7 (in days)) / 365 = 38.36
The date to order is 8th, for 2000 pieces of lot size as the total storage cost gets more extensive than the lot size-independent price of $100.
Though this example illustrates the basic calculations, the part period balancing algorithms are used in the ERP system to determine the exact lot-size holding period.
Evaluate storage cost using our Storage costs of inventory online calculator
Why Part Period Balancing?
Part Period Balancing chooses a lot size that equals the demand for storage cost to the lot size. Using this method, we can ensure the holding cost is equal to and lesser than the ordering cost.
- This method determines the excess storage cost in advance, reducing the extra cost.
- In reality, the demand for the product is uncertain and keeps changing.
- This method can be applied to the dynamically changing lot size.
- As it decides the overall minimal cost, it reduces the overall cost of the manufacturing process.
Heuristic Methods Alternative to PPB
Apart from Part Period Balancing, there are various other methods to determine the Lot Size.
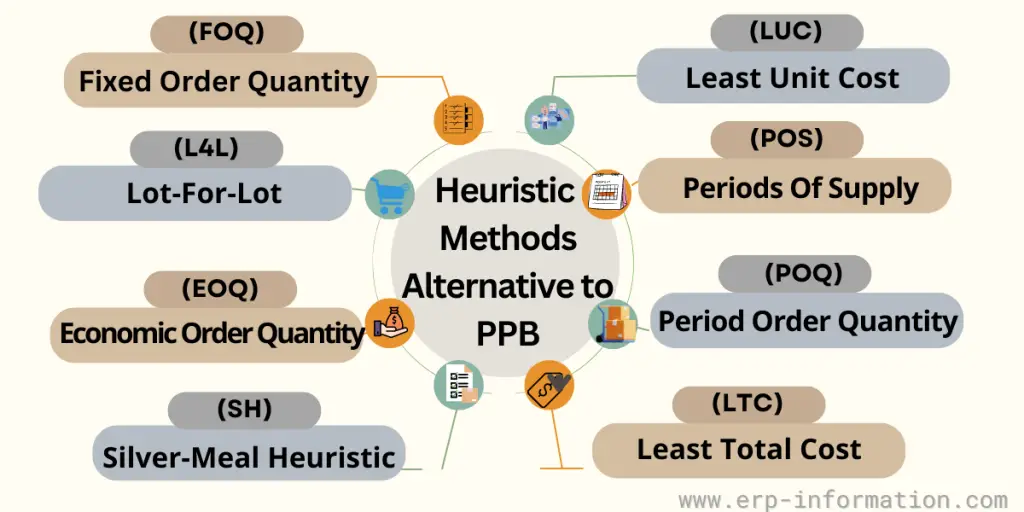
Fixed Order Quantity (FOQ): This method allows you to consider units arbitrarily to be ordered or add the lot size calculated outside the application.
Evaluate Fixed Order Quantity using our Online Fixed Order Quantity Calculator
Lot-For-Lot (L4L): This is planned according to the required quantity. The system creates the proposal as per the quantity needed for every requirement.
Economic Order Quantity (EOQ): Economic Order Quantity calculates the lot size based on the average demand over the period.
This method increases the cost by ordering the units for the next period by increasing the holding size.
Evaluate Economic Order Quantity using our Online Economic Order Quantity Calculator With Graph (EOQ Calculator)
Silver-Meal Heuristic: This determines the best lot size holding period by examining the inventory cost.
For example, I am considering period k, where k>0, the average holding and ordering cost is calculated for all the k periods until the average price per period increases.
The best k is the last one where the average cost per period decreases.
Least Unit Cost (LUC): This includes the lot size that equals the demand of the future periods.
Though there are various heuristic methods to determine the correct lot size and hence help reduce the excess cost, the dynamics of the demand and supply of the product also play an essential role in minimizing the overall manufacturing cost.
Periods Of Supply (POS): POS allows you to order the lot size equal to the net requirements for a given number of periods.
Period Order Quantity (POQ): This method considers the average of EOQ and allows considering the fixed amount of future periods to be included in each order. For example, EOQ / Avg. Period Usage
Least Total Cost (LTC): This heuristic method allows you to compare the carrying cost and order cost for various lot sizes and select the lot size where these costs are nearing equal.
In the current scenario, businesses experience dynamic scenarios during their growth period. Therefore, it is not possible to rely on a fixed lot size.
Selecting an appropriate heuristic method to calculate the lot size is challenging. However, Part Period Balancing is widely used as a dynamic lot-sizing technique for current and future manufacturing processes.
FAQs
What is Part-period cost balancing?
Part-period cost balancing is used to adjust accounting entries for prior periods. Part-period balancing helps to decide how much to buy. You can use a special calculation called Economic Part Periods (EPP). To do the EPP, divide the cost of buying something by the cost of keeping it. This will tell you how many parts you can carry before it costs too much.
Conclusion
During the Material Requirement Planning process, determining the lot size is an important task. In this article, we have considered one of the prominent lots sizing heuristic methods, “Part Period Balancing.”
Part Period Balancing is a heuristic method that can be used to balance your production capacity. It’s important because it helps prevent shortages and inventory overages, which are costly for businesses of all sizes. PPB takes into account the finite lifecycle of products as well as their lead times.
The key takeaway is that many factors are at play in making good decisions about balancing production capacity using the Part-Period Balancing Heuristics Methodology.