Net requirements are essential for ensuring that a company has the right stock on hand, but they can be difficult to calculate.
Without accurate net requirement calculations, it’s easy to have too much or too little stock on hand. That can lead to missed sales opportunities and shortages.
Net-Requirement is a tool that makes it easy to calculate your company’s net requirements accurately. With this tool, you’ll always have the information to keep your supply chain running smoothly.
In this blog post, we will explain what a net requirement is, its planning, formula, and how to calculate MRP with an example.
Calculate net requirements using our Online Net Requirments Calculator
Introduction
Net requirements are the requirements for an item based on its gross requirements (from forecasts, customer orders, or upper-level demand), minus stock already on hand and scheduled receipts.
We can calculate the net requirements either by looking at the immediate needs for production or from historical data.
When calculating net requirements, it is essential to consider all the components of a company’s supply chain and how they might affect one another so as not to run out of stock while waiting for an upstream supplier.
The goal is to produce enough goods to meet customer orders with minimal inventory. This process starts by calculating all the materials needed for production and then determining how much raw material or work-in-process can be produced within a given period.
Generating a new planned order for a given net requirement is usually done only after calculating the effect of rescheduling all incoming receipts to the dates required.
(A planned order is generated based on the lot size if the total is below the specified safety stock.)
Before talking about the net requirements, let us clarify our concept about a few terms.
Terms are gross requirements, scheduled receipts, on-hand inventory, and the projected available balance.
The first thing a firm needs to figure out before operating is its capacity. Then, the firm can easily calculate the total input or gross requirements from this value.
The term gross refers to the total estimate of material requirements a company must put in for smooth functioning in one production cycle. The gross requirement for a company is generally fixed and predetermined.
Scheduled receipts let you receive payments according to a preset schedule. For example, you can set up your account to receive customer payments every Monday morning. It is handy if you need to budget your cash flow or have other periodic expenses.
On-hand inventory refers to the stored finished goods ready to be delivered at any time. Inventory is a broader term and refers to storing various other items or raw materials.
Companies can even stock up their inventories, anticipating a massive sale before the festive season. A company with an efficient and far-sighted inventory management and control system is always ahead of its competitors.
Net requirements planning
The main problem in this industry today is that companies have not been able to keep up with supply and demand trends due to being unable to accurately predict what customers want from one year to the next.
One solution is implementing net requirements planning, which utilizes statistical analysis techniques like linear programming models.
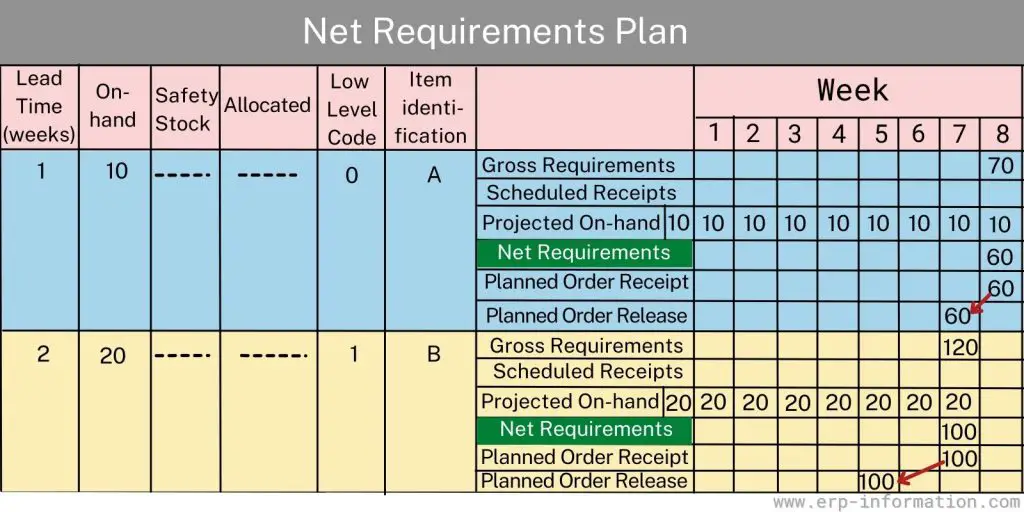
Net requirements are the material required for the coming productive period after netting the added values of scheduled receipts and the on-hand inventory from the gross requirements.
We add up the orders scheduled to arrive and the material in-store and subtract them from the gross requirements.
After netting, this value is the total amount of materials we need for the next production cycle. Again, a simple net requirements formula can explain that.
Net requirements formula
Net requirements= Gross requirements- (Scheduled receipts+ On-hand inventory)
We calculate this value meticulously by looking into the scheduled receipts and on-hand stock. Hence, it is not an arbitrary value and is not fixed for every production cycle.
Now, the net requirement amount must be above a specified safety stock. After comparing the net value obtained, this value we get with the safety stock of the firm is referred to as the projected available balance.
If it is below the safety stock, an order for more raw materials and inventory is put through.
The projected available balance is the amount of stock being projected into the future. It is like the amount of stock inventory we carry to the next production cycle from the last production cycle.
If the projected available balance is
- Zero, or
- Less than zero
An order for a planned release of materials is put up. That ensures a continuous material flow into the production line.
Evaluate Safety stock using our Online Safety Stock Calculator
MRP calculation example
Let the on-hand inventory present at a given moment be 40, and the demand for the first week is 45.
As the demand exceeds the projected balance, the entire amount of materials is used up with five more units.
That makes the projected available balance for the next week negative (-5). The net requirement for the next periodic cycle is (-5) +45= 40.
As the projected balance is negative, a planned order is released of 60 units, making the balance 55.
Now, this week, there is a demand for 40 units. That makes the projected available as 15. As the projected availability is now positive, no more order needs to be released for this particular period.
Why is it calculated?
- You must appropriately calculate the net requirements to maintain an uninterrupted workflow, and
- To manage a stable and hazard-proof inventory management control system
Thus, the net requirements of a firm are just as necessary as the gross requirements, and they must be calculated efficiently to design an efficient production line.
FAQs
How to calculate net requirements in MRP?
MRP is a production planning system. It calculates net requirements in many different areas, including raw materials and parts on order, finished goods inventory on hand, or needed to fill customer orders.
Work in progress inventory on hand, or needed for completing current jobs while minimizing the total cost of operations over time by balancing demand with supply at each step of the process.
To calculate net requirements in MRP, calculate total requirements, including physical and virtual material demands over time.
Then use your forecasted production levels to determine how many units of each type you’ll need (i.e., on order). Then, subtract what you have on hand against the total requirement figure to get your net requirement figure; this will tell you what additional materials are needed to keep things going.
How are gross-to-net calculations processed for MRP?
Gross-to-net calculations are processed by subtracting the cost of goods sold (COGS) from the company’s revenue.
This calculation results in the company’s net income, which is then used to calculate the company’s earnings per share (EPS).
We can simplify the calculation further by dividing COGS by revenue. This division results in the gross margin percentage; a key metric companies use to measure their profitability. The higher the gross margin percentage, the more profitable a company is.
How can net requirements be implemented in a planning process?
Net requirements are a critical aspect of planning to ensure you have the right amount of inventory.
By subtracting what’s already available and what’s on order from the total needed, you determine exactly how much you should order to meet future demand while preventing overstocking or shortages.
How often can net requirements be determined?
The frequency of net requirements calculations depends on your business dynamics. Regular reviews are essential to adapt to changing demand patterns.
For items with stable demand, monthly or quarterly reviews may suffice.
However, for volatile items, more frequent assessments, like weekly reviews, may be necessary to keep inventory aligned with demand.
How can net requirements be employed to enhance business efficiency?
Adopting net requirements can yield improved business efficiency through the following approaches:
Minimizing inventory costs by preventing excessive stock levels.
Enhancing customer service by mitigating the occurrence of stockouts.
Streamlining the operations and reducing lead times by proactively ordering materials and products ahead of time.
Conclusion
Net requirements help accurately assess what’s needed before any manufacturing occurs.
The net requirement helps avoid overproduction, underproduction, and excess inventory costs associated with these problems. It also saves on storage space by not ordering more products than necessary.
Still, at the same time, it ensures there’s enough material available if production needs increase unexpectedly or demand increases during certain seasons or marketing campaigns.
Other benefits include improved customer service due to better forecasting, increased responsiveness to spikes in demand, and reduced lead times.