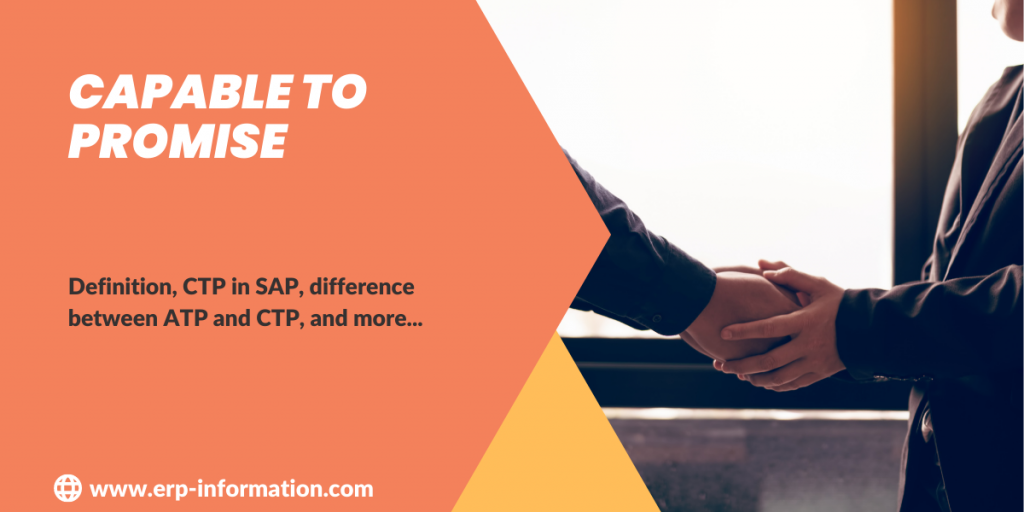
Capable-To-Promise (CTP) measures the amount of work an organization can commit to in the near term. It’s calculated by subtracting the amount of work already in progress from the total amount of work available to be assigned.
A company can use an organization’s CTP to measure its ability to meet customer demand in the short term. It can also be used to help prioritize assignments and manage workloads.
This post gives you a clear idea of CTP with examples, limitations, and differences with available-to-promise (ATP).
Capable-To-Promise definition
It is the process of committing orders against available capacity and inventory. This process may involve multiple manufacturing or distribution sites.
It determines when a new or unscheduled customer order can be delivered. It employs a finite-scheduling model of the manufacturing system to determine when an item can be achieved.
It includes any constraints that might restrict production, such as the availability of resources, lead times for raw materials or purchased parts, and requirements for lower-level components or subassemblies.
The resulting delivery date considers production capacity, the current manufacturing environment, and future order commitments.
The objective is to reduce the time spent by production planners in expediting orders and adjusting plans because of inaccurate delivery-date promises.
What is Capable-To-Promise (CTP) manufacturing and how does it work?
Capable-To-Promise (CTP) manufacturing ensures that a business can confidently commit to or decline customer orders based on its current production capabilities. Using a “finite-scheduling model,” CTP considers all constraints, such as raw material availability, staff capacity, inventory levels, equipment status, and overall production capacity. By leveraging ERP software like Acumatica, businesses track these factors precisely:
- Raw Materials: Monitor exact quantities of input materials using unique codes.
- Staff: Assess production speed based on the number and skills of employees.
- Inventory: Use warehouse management systems (WMS) to track stock locations and shipping times.
- Equipment: Identify operational status and efficiency of machinery to predict lead times.
- Capacity: Determine current production levels and available capacity for new orders.
Limitations
- It is not easy to use this process to schedule a complete Supply Chain Plan.
- It is not usable for delivery document checking.
- Some of the factors negatively influence the performance of the process, like a large number of lots to be created, a large number of resources, and a large number of activities per order.
- It is not suitable for SD delivery schedules.
- It is not suitable for backorder processing.
What is Available Capacity?
Available capacity is the process that involves the determination of the potential of a unit to perform a specific task within a set time framework. The capacity to deliver an expected output varies from industry to industry.
Based on the business, the available capacity has to be ascertained. Then, it can work in terms of volume quantity and compare the same with the standard available capacity of the firm.
A company can determine the available capacity for a single resource or a set of resources. The process helps in overall business planning and inventory management.
Differences between Capable-to-promise and Available-to-promise
(What is Available-to-promise (ATP)? – It is a term used in sales and operations planning that refers to the total quantity of products or services available to be shipped to customers at any given time, minus the quantities currently held by or committed to other customers.)
ATP | CTP |
It considers only material availability | It considers both capacity and material availability. |
It does not provide a realistic view of the capability of demand fulfillment within a given period. | It gives a clear idea about the capability of demand fulfillment within a given period. |
Calculation of ATP is simple and takes less time. | Calculation of CTP is a bit complex and takes more time. |
Example
An example in manufacturing is when a company agrees to deliver a product on time and to specification.
This means that the company has the resources to make good on its promise, and it also indicates that the company is confident in its ability to produce a quality product.
When a company makes a CTP pledge, it puts its reputation on the line. So it’s essential for companies only to make promises that they know they can keep.
By doing so, customers and suppliers can have confidence in the manufacturing process and be assured that the company will deliver high-quality products on time.
Let us assume X is the final product, and Y and Z are components required to produce X.
Now, suppose the on-hand inventory of product X is zero. In this case, if you do ATP, it shows zero only because it checks only the availability of the material.
If you do CTP, it shows the availability of both materials and available resources. So it determines the availability of components Y and Z to make product X.
It also checks the number of products produced using these materials and resources. It also limits how many more components Y and Z and other resources are required to make more product X.
Determining the ideal working hours
The working hours of an organization are crucial to determining the unit’s production capacity.
However, the working hours comprise the breaks, technical glitches faced during those hours, and any organizational problems.
Cracks are generally deducted to attain the working hours. Thus, they are also known as the theoretically available hours.
The productive working hours gained after deducting the technical and organizational problems are known as the operating time.
Similarly, capacity utilization can be used to understand the percentage of the running time of a unit in production.
The differences obtained while calculating the available capacity are known as the version number. The actual version number is further used in scheduling and planning capacity requirements.
FAQs
What is Capable to Promise in SAP?
CTP is a function in SAP that allows you to specify the delivery conditions for a sales order. With this, you can indicate to your customer that you can deliver the goods within a certain time frame and under specific conditions.
This helps ensure that your customer knows what they can expect from you, and it also limits your liability if something goes wrong with the order.
It is available in all versions of SAP ERP and can be used for goods and services. Setting up it is pretty straightforward, and plenty of online resources help you get started.
Conclusion
CTP is a process that helps determine when an order can be delivered to the customer. It involves multiple manufacturing or distribution sites and employs a finite scheduling model to determine when an item will be achieved.
This article has provided information on what this process entails and how it may benefit your business strategy. We hope it was informative.